As the core part of the hydraulic end of the plunger pump, the emulsion pump head is under a lot of pressure. Therefore, the finite element analysis of the pump head is of great significance to improve the reliability and rationality of product design.
Due to the special structure of the emulsion pump head, researching its processing technology and improving processing efficiency is the key to reducing production costs and improving product competitiveness. The motion law of the plunger pump, the pulsating flow and the pressure fluctuation caused by the pulsating flow are analyzed, and the relevant factors causing the pressure fluctuation are obtained, which provides a theoretical basis for the design and improvement of the plunger pump, and also provides a basis for analyzing the pressure of the pump head. The force state provides an important theoretical basis.
The stress distribution law and fatigue life distribution state of the emulsion pump head under the larger stress state are analyzed, and the improvement measures of the pump head structure are proposed according to the analysis results. According to the working conditions and structural characteristics of the pump head, the process route of the pump head from material, blank, large-diameter hole nesting, turning stepped hole, milling inch thread, rolling to hydraulic self-enhancement is given. The characteristics of the nesting drill are emphatically analyzed, the structure type of workpiece rotation and external chip removal is selected, and the drilling related technologies of the nesting drill are analyzed in detail, such as cutting power, cutting parameter selection, cooling and chip removal, as well as the nesting drill. The difference from ordinary hole processing.
Tool parameters are an important factor affecting the machining efficiency and service life of the tool. Since the nesting drill works in a closed space, under the premise of satisfying the processing efficiency, determining the method of chip breaking and chip removal is the key to the design of the nesting drill.
In addition, the influence of the axial vibration of the tool on the cutting angle during the drilling process is analyzed, and the theoretical basis of the influencing factors of the hole axis deviation is given. Milling is used to process inch threads, and the application of macro programs improves the efficiency of thread milling. In order to improve the strength and service life of the pump head, the inner cavity is prestressed by the hydraulic self-enhancing method of the inner hole.
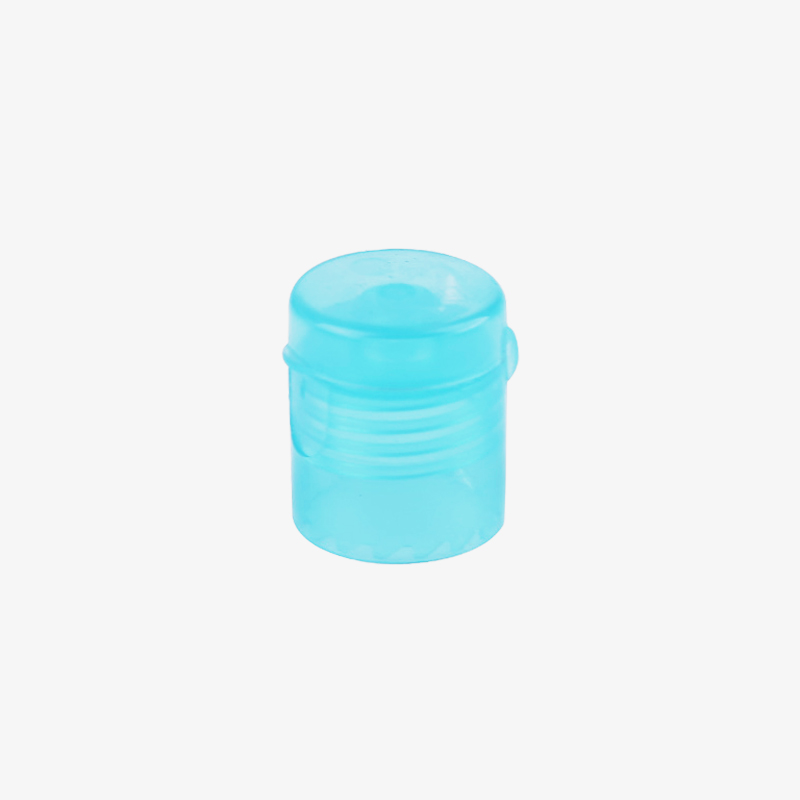
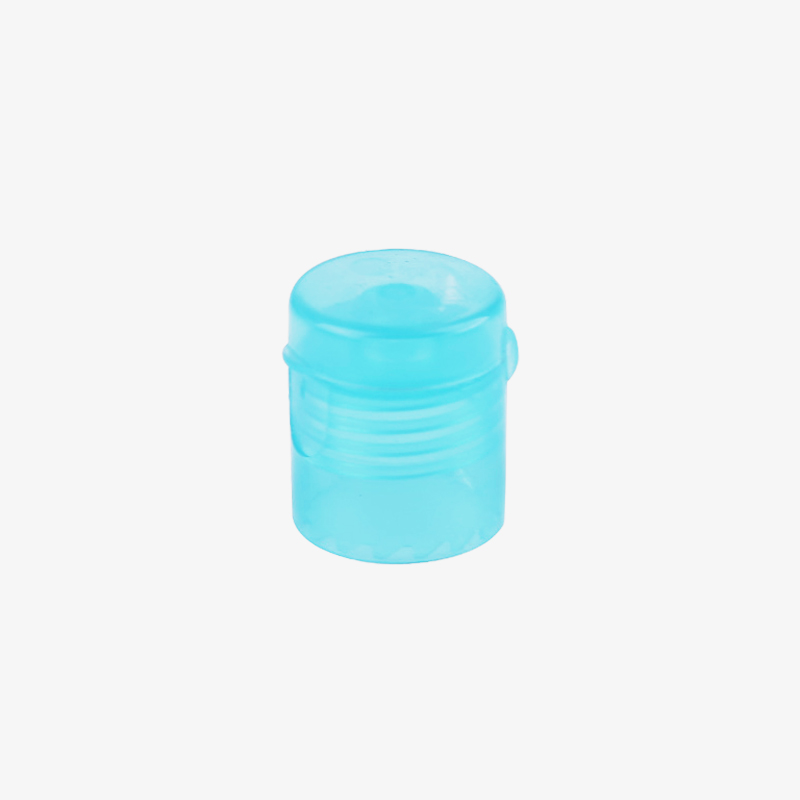